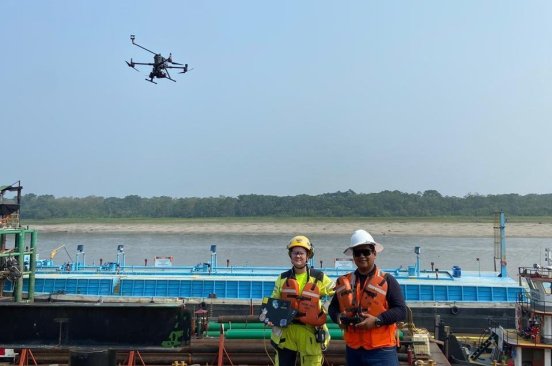
Pakistan Flying Labs Explores the Usage of Drones in Non-Destructive Testing of Industrial Infrastructure
By removing the need for inspectors to enter potentially hazardous restricted locations, drones enhance safety, increase efficiency, and ensure data accuracy.
September 21st, 2023
Non-Destructive Testing, or NDT for short, is a method of inspecting a material or structure without causing any harm to it in the process. Using NDT, you can analyze a chemical without damaging it. One subset of NDT, Ultrasonic NDT (UT), is increasingly used in industrial drone settings.
The primary distinction between NDT and Destructive Testing (DT) is that inspectors are not required to destroy test materials in the former. DT methods, such as macro sectioning, tensile testing, or three-point bend testing, involve physically modifying or removing a material sample from its original location.
Why go with Non-destructive Testing?
Non-destructive testing is crucial to ensuring that machinery is in good working order. There are several primary drivers behind its widespread adoption.
NDT is preferable to destructive testing because it saves time and money by allowing the tested material or item to remain undamaged during inspection. Except for X-rays, all NDT methods are perfectly safe for human beings to be exposed to, making NDT an especially intriguing field of study.
Non-destructive testing techniques also allow for the thorough and fast assessment of assets, which is often crucial to guaranteeing the security and effectiveness of a project.
Furthermore, NDT procedures are reliable and consistent, both of which are important qualities in preventative maintenance that aim to protect workers and prolong the life of their equipment.
When is NDT employed?
Since visual inspection (formal or incidental) occurs in some shape or form in practically every workplace, non-destructive testing is likely used in virtually every industry around the world. However, several sectors insist on non-destructive testing and employ well-established protocols.
Ultrasonic NDT is necessary in the following industries:
- Energy (oil and gas)
- Production of energy
- Synthetic substances
- The mining industry
- The aerospace industry
- Motor vehicles
- The seafaring
All of these industries' inspectors rely on one of three approaches to reach inaccessible or elevated areas:
- Scaffolding: Scaffolding inspections typically involve inspectors working at height.
- Access via rope: Rope access inspections require inspectors to work at height.
- Drones: Drones allow inspectors to safely conduct inspections without entering potentially dangerous or confined situations.
Applying Unmanned Aerial Vehicles (UAVs) in Non-Destructive Testing
Drones with built-in cameras have been increasingly used in NDTs in recent years. For now, drones can only supplement human inspectors by providing them with more visual data, but they can only partially replace them. However, with the advancement of drone technology, inspectors might soon use drones in this capacity. There are a growing number of Remote Visual Inspection (RVI) solutions that can reduce or even replace the need for human observers to collect visual data physically.
Safety
By removing the need for inspectors to enter potentially hazardous restricted locations, drones contribute to a safer work environment.
A UAV may collect visual data from objects like electrical wires or poles in a fraction of the time it would take a human to fly over a tower or line physically. Drones can safely inspect internal objects like pressure vessels and boilers without the inspector risking injury by entering confined locations.
Non-destructive inspections are the safest and most effective option when looking for flaws that could cause dangerous situations, breakdowns, or catastrophic failures. They lessen the likelihood of mishaps during test operations when workers attempt to enter hazardous or inaccessible areas. Traditional destructive testing methods, such as welding or using open flames, pose fire and other hazards, but they can be avoided using this method.
Preventative maintenance is also possible, thanks to early error detection. This eliminates any potential for interference to cause fires or other incidents that could harm workers or nearby residents.
Minimizing Downtime
Indoors and out, businesses can benefit from drones by increasing their return on investment (ROI). Drones can do non-destructive testing on materials, making it simple, fast, and cheap to find imperfections. As a result, technicians can make necessary fixes and swap out worn parts before problems even emerge. During non-destructive inspections, they can also go into tight spots that would otherwise require a large vehicle or a helicopter.
In their own ways, these technologies help reduce the time and money needed to conduct various types of inspections. Continuous testing of processes also helps reduce wasteful breaks in production.
Reliable Inspection Data
Using a drone, NDT can check facilities and offer details that would take days to acquire using conventional access techniques. Drones can deliver accurate and reliable test data for various attributes in the oil and gas industry. The inspection procedure is frequently repeatable, which is great because it can be quite helpful in gauging the success of a repair. Drones may use GPS and other characteristics to recreate a scene from the same vantage point. As a result, maintenance workers can gather reliable data and avoid mistakes from conducting tests in various settings.
Reduced Housing and Subsistence Costs
Since drone testing takes less time, companies conducting NDT save money on housing, perks, and transportation costs.
Drones equipped with NDT equipment can detect leaks and other pipeline damage early on, allowing maintenance workers to take corrective action. Faster inspections are possible using drones, which means problems may be found earlier, and assets can be maintained longer. In one study, these preliminary findings could save businesses hundreds of thousands of dollars.
Ultrasonic Inspections Through UAV
Drones with ultrasonic thickness gauges can ignore paint coats while measuring metal thickness by touching test surfaces.
Drones have many advantages over more traditional forms of inspection, making them a good choice for a wide variety of uses. The benefits of using these drones for non-destructive testing in the industrial setting are growing rapidly. By combining drones with non-destructive testing, you may reap the benefits of both the drone's portability and the inspection's lack of irreversible damage. This improves safety, saves money, and keeps test materials from being tampered.
If done correctly, an NDT drone inspection can preserve structures while providing valuable insight. However, familiarity with the activity and the nature of the sought-after data is essential. Understanding the potential and the constraints is crucial. In addition, you must have a firm grasp of the test's fundamental requirements and guidelines.
Our Experience
Earlier this year, Pakistan Flying Labs Director, Mr. Obaid ur Rehman, piloted and facilitated a drone-based visual and UT inspection for EEPCON Pvt. Ltd. at one of their clients' Industrial Process Plant in Karachi, Pakistan. This was the first time this kind of drone-based UT NDT inspection was performed in Pakistan. For this purpose, a UT NDT Kit supplied by Tritex UK was used and integrated with a DJI Matrice 300. The visual inspection was performed by using DJI Mavic Pro 2.
The inspection results were astounding and gave the client a detailed overview of the health of their assets and guided prompt decision-making to perform remedial actions at their Industrial Process Plant. This application proved reliable and saved significantly on both time and cost.
From our experience, drone-based NDT inspections are a valuable investment as they lessen the danger to the NDT technician and, in some cases, allow the NDT specialist to reach important spaces that would otherwise be inaccessible.
Category(s)
Location(s)
Recent Articles
View All »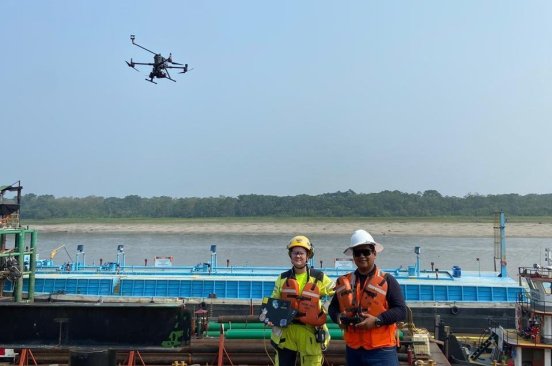
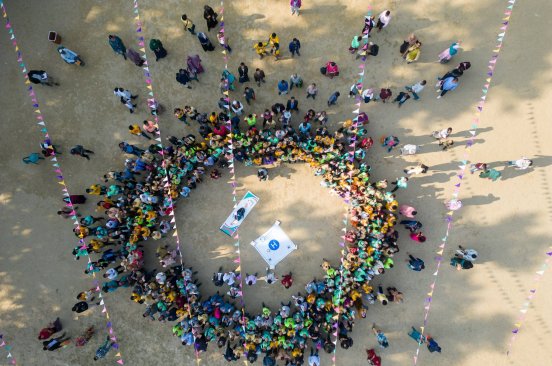
Bangladesh Flying Labs at the National Math Olympiad 2025
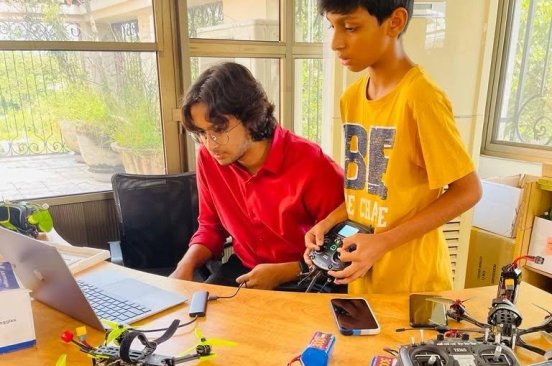